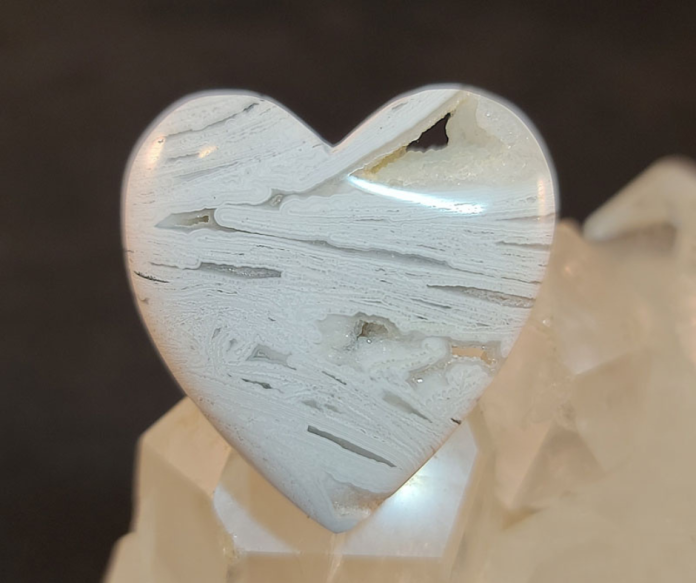
Mexican lace agate, a stone that has no color hues, can quickly remind you of a snow-covered pine tree, or the feathers of a swan. Lace agate makes up for its lack of color in the beauty of its feather-like patterns. This material comes from Mexico and has many of the same compounds as crazy lace agate without iron-infused colors.
Buying & Picking Material
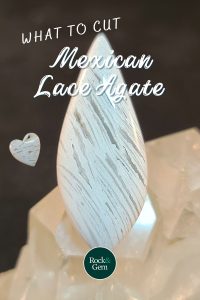
Even though Mexican lace agate isn’t readily available, it can still be found in online sales or at shows. When picking out material to slab, you can see how the patterns will look from the outer sides of the rough. The rough may vary from tightly compressed sagenite lines to many open drusy vugs. Most of the material that I have encountered has been stable and fracture-free, but with all stones, there are still chances of finding fractured material. Just look carefully before buying.
When starting to slab the stone, look for the side with the best patterns and directional patterns that you like best. There’s a good chance, you will only cut maybe a slab or two, before wanting to pull the rough out and reposition it in the saw and try from another side. With each slab cut, the patterns and direction of the patterns will completely change, so it might be best to experiment with cutting from different sides to find what you like best.
Preform & Cabbing
When starting to draw out preform shapes, give an extra 1mm of space around your design, as this material tends to be a bit delicate around the edges and can chip on the coarser grit wheels. This will leave extra room to fix what might be lost to a chip.
As with most agates, most people start off on an 80-grit steel wheel, but with this material, I would suggest using a broken-in wheel, and not one that is brand new, as it will chip the edges. I would suggest using the 80-grit to shape somewhat close to your drawn-out lines and then graduating to a 60-grit soft resin wheel to finish shaping the edges. You can go back to the 80-grit to dome the top or take a little extra time and do it on the soft 60-grit wheel.
From this point, you can use a soft 140-grit, which would help to speed up production or go to your 280-grit soft resin wheel. This is where you want to take your time and make sure all the scratches are out. There is one very big pitfall. White stones are the hardest to see scratches in, especially if they have sagenite patterns. One thing you can try is to quickly jump to your 1200 soft resin wheel and run your cab over that for a minute. It should show you any/all the scratches that are still left.
If they are all gone, consider that finished at the 280-grit stage and move on to your 600-grit wheel. From this point, this material will still look dull, but don’t let that fool you. It will start to show a dull shine on the 1200-grit stage. I usually finish up on either an 8k-grit soft wheel or step it up a notch for a more mirror finish on the 14k-grit wheel. Just be careful. Even on the fine polishing wheels you can still crack or fracture a vug that’s close to the edge of your cab.
For most people, finishing on the wheels will leave a beautifully desired polish. For those who want to obtain a super glossy mirror finish, you can use either cerium oxide on a leather buffing wheel or Zam polishing compound with a felt tip on a Dremel or a foredom tool.
This story about mexican lace agate previously appeared in Rock & Gem magazine. Click here to subscribe. Story by Russ Kaniuth.