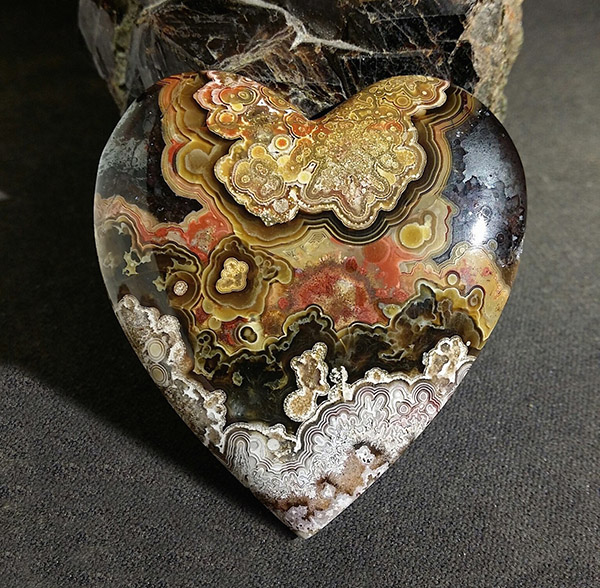
by Russ Kaniuth
Mexican Crazy Lace agate is probably the best known and most widely used lapidary material since the 1950s. Whether it’s because of its various colors, sagenite sprays, translucent waves of colors with parallax, bull’s-eyes, or paisley-looking patterns with bright colors, Crazy Lace agate sure lives up to its name!
Mexican Crazy Lace agate comes from the state of Chihuahua, where the agate is embedded in limestone. Due to the mining techniques used and how the agate is encrusted with the limestone, it can be very hard to find solid pieces yielding whole patterns. What I have seen in the marketplace within the last five years is mostly fractured; however, since there’s always so much going on with the patterns and colors, it’s still fairly easy to find really good sweet spots in the slabs to make cabs from.
Crazy Lace is usually slabbed by cutting against the grain so that the waves of colors are showing. This is pretty easy to figure out how to do; if you wash off the piece, you can usually see which direction the patterns are running. This is not the only way to cut this material, though.
When you are ready to buy and are sorting through rough material, sometimes it’s best to know what you’re looking for. For instance, when a piece has a botryoidal side, there’s a good chance that if you slice that end section off and grind down a little way, you will obtain a very different pattern with “bull’s-eye” orbs. In my opinion, this is one of the most beautiful patterns you can achieve when cutting Crazy Lace.
Not all the material will have that layer, but it’s much like a treasure hunt, in which you keep cutting until you find your favorite piece. As with any material, when cutting, always wear a respirator mask to avoid breathing in any of the dust.
Cabbing Crazy Lace isn’t all that difficult. It’s a hard material, so it takes time and patience, but overall, it’s one of the nicest materials to cab. Grind the top edges of the waves slowly and not too aggressively, since doing so might cause it to separate between layers. I’ve had this happen many times. In fact, it usually will separate cleanly on a botryoidal layer within the stone. You can use that as a natural edge to your cab for a nice effect, or you can always epoxy the two layers back together and, after the glue cures, go back and resume grinding where you left off.
When you’re starting on the wheels, this material will cut and shape cleanly, but be sure that you have removed as many of the flat spots and deep scratches from the cab as possible by the time you reach the 220 grit. Then, once you move on to the 280 grit wheel, be sure to dry the cab off often and check your progress. You should not leave this stage with any scratches whatsoever.
From this point on, the cabbing process should be rather routine. The stone will even look almost completely done after the 1200 grit wheel, but I would suggest going up to as high as14000 to 50000 grit polishing wheel to get that remarkable mirror shine to your work. With Crazy Lace, there’s usually no need to go to any extra polishing agents, but depending on the material, sometimes you may need to polish on a leather buff with cerium oxide to gain that little added touch!